A Tool Inventory System to Improve Oil & Gas Jobsite Management
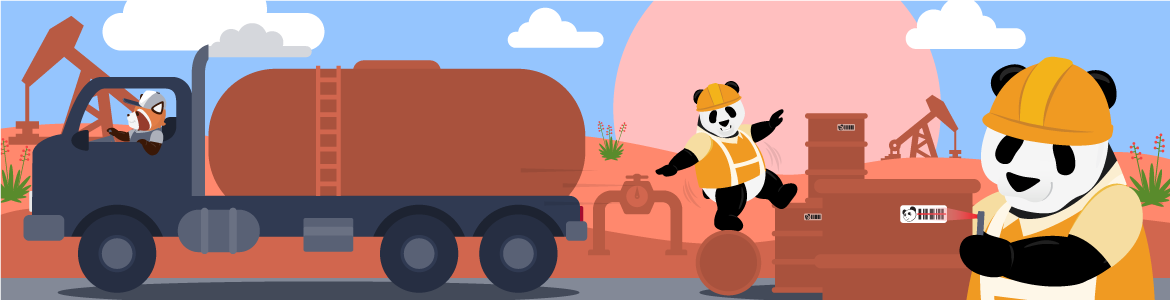
Take Control of Your Assets
A personalized demo is just one click away.
A tool inventory system may seem like a simple improvement to your organization’s workflow, but it can actually be a transformative change that improves the efficiency, safety, effectiveness, and profitability of your business.
In the oil & gas industry, this is especially true. With multiple job sites, countless power tools across several locations, and the need to say on-task and on-schedule, knowing what tools you have available, where they are, and whether they’re in functional working condition is absolutely essential.
But what exactly is a tool inventory system, how do they work, and how can you harness the best platforms to your benefit? Here’s everything you need to know about tool inventory systems for oil & gas industry businesses.
What is tool tracking software?
Tool tracking software is a system used to store information about the full lifecycle of the tools owned and used by a business. These systems provide teams with the ability to share information across job sites and keep track of things like maintenance requirements, warranties, required training, and tool availability.
Tool inventory tracking involves applying a unique barcode to every tool and piece of equipment across all of your job sites. This helps companies know exactly what they have, the condition it’s in, and where it should be located so they can be prepared for projects and eliminate inventory surprises.
The ability to view inventory across multiple sites is especially helpful, allowing managers to immediately determine where a tool is needed and if one is unavailable. Check-ins and check-outs are easy to monitor and help establish accountability.
With real-time, accurate information, companies can make informed decisions about what they need to order and when. They don’t order tools that aren’t necessary. Budgets are especially critical in the oil and gas industry because every project has unique variables and requirements.
How a Tool Inventory System Works in the Oil & Gas Industry
Tool inventory software continues to raise the standards for job site management by helping save millions of dollars in lost equipment, tools, and maintenance.
A 2019 McKinsey Global Institute report stated that, while productivity within the oil and gas industry has grown, it remains behind sectors like manufacturing and retail. Among the management practices and technologies that may improve capital-project performance, the report says, is the implementation of more digital technologies. Tool inventory software is a giant step in the right direction for the oil and gas industry.
The average oil and gas company is responsible for managing multiple job sites. Each of those sites need properly maintained tools to increase worker safety, performance, productivity and company morality.
Improving Productivity with a Tool Inventory System
One of the most powerful benefits of an accurate tool inventory system is the way that it will boost the productivity of employees and job sites. When everyone knows where specific tools are located, whether they’re functioning, and whether they’re currently available, imagine the reduction in wasted time. No more grinding to a halt on a project because a certain tool that was expected to be available is no longer usable. No more putting work on hold while team members search multiple job sites for a tool that’s essential to get the job done.
Meanwhile, maintenance schedules for tools can also be tracked, which means you won’t have to unexpectedly take a tool out of use while it can be repaired. All of those unexpected delays can add up to significant hits to your overall productivity, and that adds up to real costs for your organization.
Reducing Cost with Efficient Tool Tracking
Speaking of costs, an efficient tool inventory system can help save money at your company in other ways.
One of the most powerful benefits of accurate and organized tool tracking is that there’s never any confusion about which tools you own and can use, and which ones you don’t or which are unusable due to damage.
On countless occasions, companies order a tool that they can’t find only to later discover that they had the tool all along, perfectly functional but simply lost because they had no accurate tool tracking system in place.
Accessibility Through Mobile Tool Inventory Management
Mobile technology is a complete game-changer for tool and equipment tracking and maintenance. Workers may request tools from the field with a smartphone or tablet, monitor the status of repairs or orders, and cut down on wasted time and money. Asset Panda’s tool inventory software syncs with the cloud and is powered by a mobile app with a built-in scanner. Everything oil and gas companies need to track and manage the lifecycle of their job site inventory is centralized within the app for anytime access.
Safety and Your Tool Inventory System
Safety can’t be emphasized enough, and digital technology holds significant value in that area. Tool inventory software allows companies to set up custom notifications and alerts so they can keep up with routine preventive maintenance. It also enables companies to maintain a record of employee training so they can ensure that tools are only being used by qualified team members.
Of course the physical safety and wellbeing of your employees and job sites is the top priority by a large margin. But enhanced safety through the use of careful tool maintenance and condition tracking is also a cost savings measure— legal liability for injuries and the costs of a job site being shut down after a safety incident can all be devastating for companies of any size. Keeping your tools in working order by accurately tracking them using a tool inventory system can help insulate you against these financial risks, too.
Reduce Theft of Tools
Theft is a common concern for any company that maintains a large inventory of expensive tools and equipment. When a barcode attached to an asset is scanned, you can collect the GPS coordinates of the smartphone used to scan it, putting a pin on its location for future reference.
This means that you can create a clear path of use and accountability for your tools. Asset tracking platforms like Asset Panda allow users to ‘check in’ and ‘check out’ tools, which means that you can quickly look at a tool’s history to see who accessed it last— and who had ownership of it when it went missing.
This level of accountability can help deter theft and poor treatment of your company’s tools and other assets— and help get to the bottom of cases of theft or other mistreatment.
Track from Anywhere, Not Just in Your Own Facility
Tracking that uses mobile devices as scanners and a cloud-enabled platform means that you don’t have to be at your own facility to access information relating to your tools. If you have a smartphone and internet access, you can open your asset tracking app from anywhere in the field or on a job site and instantly scan a barcode or search for information about tools on other jobsites.
That cuts down on traveling to job sites on the hunt for a tool and digging through complicated spreadsheets that may or may not be up-to-date as it relates to tool information.
Track Past and Present Data
One of the most significant benefits of an asset tracking platform is the ability to track and analyze present and past data. This lets you track a tool’s history, and the history of all your assets as a whole, to identify trends in the way you purchase, use, maintain, and replace assets throughout your organization. This can be an invaluable tool for helping you make future buying decisions, adjust and implement policies for asset management within your business, and much more.
Compliance and Accounting
A tool inventory system powered by an advanced asset tracking app will also allow you to instantly generate reports, which can be shared with stakeholders and include information like total tool assets, value, where they’re assigned, their maintenance schedules, and more. This provides visibility and increased accountability as well as the chance to show relevant stakeholders that you’re invested in your organization’s important physical assets.
This reporting is also essential when it comes to accounting requirements and compliance, both with tax regulations, industry regulations, and other relevant measures that govern your business or industry.
Conclusion
Are you ready to implement a tool inventory system that will make your business more efficient, cost-effective, compliant, productive, and safe? Asset Panda is one of the most trusted asset tracking solutions for businesses of all kinds, with a fully configurable interface that lets you track exactly the information that matters most to you.
Find out how Asset Panda can transform your business. Get a demo today!
Take Control of Your Assets
A personalized demo is just one click away.
Related News & Press
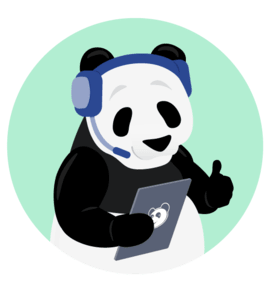
Learn more from an Asset Panda expert
Get a FREE consultation with an asset tracking expert to find out how you can transform your asset tracking.
Contact our Sales Team at (888) 928-6112